다이캐스팅 Die Casting - 역사, 원리, 공정 단계 및 종류
2025. 3. 19. 02:24ㆍ과학-기구
반응형
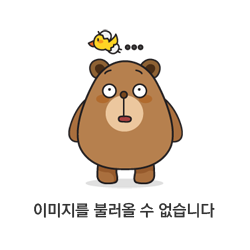
다이캐스팅의 역사
1838년 Ge Bruce가 다이캐스팅을 통해 처음으로 서체를 제작했으며, 1839년에는 피스톤 다이캐스팅 머신이 최초의 압력 캐스팅 특허를 획득했습니다.
1849년 영국의 Sturges가 핫 프레스 챔버 다이캐스팅 기계에 대한 특허를 획득했고, 1885년에는 O. Mergensel이 개선된 다이캐스팅 머신을 사용했습니다. 1907년 Wagner는 공압 피스톤 다이캐스팅 머신을 발명했습니다.
현대적인 다이캐스팅 기술의 발전은 1925년 독일의 Electronmetal사가 시계 최초로 마그네슘용 다이캐스트기를 개발하면서 본격화되었습니다.
1927년에는 체코의 Joseph Polak이 수직 냉간 챔버 다이캐스팅 머신을 설계했고, 1953년 미국의 Dow Chemical사가 핫 챔버기 특허를 출원하면서 핫 챔버 방식의 발전 시 시작되었습니다.
다이캐스팅의 정의과 기본 개념
- 다이캐스팅은 고압을 사용해 용융된 금속을 금형에 주입하여 복잡한 형태의 금속 부품을 빠르고 정밀하게 대량 생산하는 금속 주조 공정입니다.
- 영어 단어 Die금형와 Casting주조의 합성어로, 말 그대로 금형을 사용한 주조 공정을 의미합니다.
- 다이캐스팅은 주로 아연, 구리, 알루미늄, 마그네슘, 납, 주석 및 그 합금과 같은 비철금속을 사용하여 정밀한 형태의 금속 부품을 제조하는 기술입니다.
다이캐스팅의 원리
- 다이캐스팅의 기본 원리는 고압을 사용하여 용융 금속을 정밀 금형 캐비티에 고속으로 밀어 넣는 것입니다. 용융된 금속은 압력을 받으며 냉각 및 응고되어 주물을 형성합니다.
- 위의 공정은 다른 주조 방식과 달리 고압과 고속이라는 두 가지 주요 특징을 가지고 있습니다.
- 다이캐스팅은 용융 금속을 압력 챔버에 붓고 금형의 공동에 바르게 채워 압력을 가하여 합금을 응고시켜 주조품으로 만든 방법입니다.
- 이 과정에서 금속이 다이 캐비티에 주입되는 데는 단 몇 분의 1초밖에 걸리지 않으며, 압력을 지속적으로 가함으로써 금속이 금형 전체에 골고루 채워지고 정밀한 형태로 응고되도록 합니다.
- 다이캐스팅의 핵심 물리적 원리
- 압력 전달 원리
- 다이캐스팅은 파스칼의 원리를 기반으로 합니다.
- 밀폐된 시스템에서 압력이 모든 방향으로 동일하게 전달되는 원리를 이용하여 용유 금속이 금형의 모든 부분에 균일하게 채워지도록 합니다.
- 형체력ClampingForce
- 다이캐스팅 기계에 의해 금형에 가해지는 힘이 형체력입니다.
- 이는 주조 중 캐비티 내 용융물의 분리력OpeningForce 보다 커야 하며 형체력의 공식은 아래와 같습니다.
- F=P*A - 형체력kg = 주조 압력kgf/cm2 * 총 투영 면적cm2
- 압력 전달 원리
다이캐스팅의 공정 단계
- 금형 설계
- 매우 상세하고 정호가한 금형 3D 모델을 생성합니다.
- 금형 설계 타당성을 더욱 향상하기 위해 금형 흐름 분석이 활용됩니다.
- 여기에는 잠재적인 문제를 식별하기 위해 금형 캐비티로의 용융 금속 흐름을 시뮬레이션하는 작업이 포함됩니다.
- 금형 준비
- 다이캐스팅의 핵심은 '다이'라고 불리는 특수 금형 제작에 있습니다.
- 이러한 금형은 캐비티와 코어의 두 부분으로 구성되며 일반적으로 경화강으로 제작됩니다.
- 금형은 고압과 고옥에 견딜 수 있도록 특별히 설계되며, 정확한 치수와 표면 품질을 보장합니다.
- 주입
- 용융 금속은 러너 시스템을 통해 고속 및 고압으로 금형 캐비티에 주입됩니다.
- 압력은 금속이 금형을 완전히 채우고 정확한 모양을 갖추도록 하며, 이 단계에서는 속도와 압력 제어가 매우 중요합니다.
- 냉각 및 배출
- 주입 후 금속은 닫힌 다이 내에서 냉각되어 응고됩니다.
- 냉각 시간은 사용되는 합금에 따라 달라질 수 있습니다.
- 금형이 열리고 이젝터 핀이 부품을 금형 캐비티 밖으로 밀어냅니다.
- 금형이 완전히 응고된 후에는 금형에서 부품을 제거할 수 있습니다.
- 후처리
- 주조된 부품은 원하는 최종 제품을 얻기 위해 기계 가공, 표면 마감 또는 열처리와 같은 추가 공정을 거칠 수 있습니다.
다이캐스팅의 종류
다이캐스팅은 크게 두 가지 방식으로 분류됩니다.
- 핫 챔버HotChamber 다이캐스팅
- 핫 챔버 다이캐스팅에서는 주입 메커니즘핫챔버이 용융 금속이 완전히 잠겨 있으며, 작동 원리는 아래와 같습니다.
- 저융점 합금을 핫 챔버에 넣고 녹는점에 도달할 때까지 가열합니다.
- 용해된 합금은 구즈넥 영역으로 이동하고 플런저가 구즈넥 영역 내부에서 일정한 압력으로 합금을 밀어냅니다.
- 압축된 용융 합금이 다이 캐비티로 이동하여 다이캐스팅 공정이 진행됩니다.
- 다이캐스팅 금형 캐비티는 용융된 합금을 냉각 및 응고시키며, 용융된 합금은 설계에 따라 형태를 갖추게 됩니다.
- 핫 챔버 다이캐스팅은 일반적으로, 아연, 마그네슘과 같이 용융점이 낮은 합금에 사용됩니다.
- 이 방식은 더 빠른 사이클 시간, 재료 낭비가 적은 장점이 있고, 중소형 부품 생산에 적합합니다.
- 핫 챔버 다이캐스팅에서는 주입 메커니즘핫챔버이 용융 금속이 완전히 잠겨 있으며, 작동 원리는 아래와 같습니다.
- 콜드 챔버ColdChamber 다이캐스팅
- 콜트 챔버 다이캐스팅에서는 용융 금속이 금형에 주입되기 전에 콜드 챔버에 래들링됩니다.
- 주입 메커니즘과 용해로가 분리되어 있으며, 작동 원리는 아래와 같습니다.
- 합금 재료가 용융점에 도달할 때까지 별도의 챔버나 용기에서 합금 재료를 가열합니다.
- 합금을 녹는점까지 가열한 후 국자를 사용하여 용융된 재료를 쇼트 챔버로 옮깁니다.
- 용해된 금속을 쇼트 챔버에 넣은 후 플런저 도구가 용융된 재료를 다이 캐비티 안으로 밀어 넣습니다.
- 용융된 합금이 다이 캐비티에 도달하여, 냉각 및 응고되어 최종 형태를 갖추게 됩니다.
- 콜트 챔버 다이캐스팅은 알루미늄, 황동, 구리와 같은 고융점 합금에 적합합니다.
- 이 방식은 고강도 및 내열 부품 생산에 이상적이며, 더 크고 복잡한 구성 요소를 제작할 수 있는 장점이 있습니다.
다이캐스팅 - 장점, 단점 및 응용 분야
https://baruaaaa.tistory.com/160
다이캐스팅 Die Casting - 장점, 단점 및 응용 분야
다이캐스팅의 장점고정밀 및 공차 제어다이캐스팅은 치수 안정성이 높은 고정밀 부품을 생산합니다. 기 공정은 다른 공정으로 달성하기 어렵거나 불가능할 정도로 복잡한 모양과 기능을 생성
baruaaaa.tistory.com
반응형
'과학-기구' 카테고리의 다른 글
파스칼의 원리 Pascal's Principle 1 | 2025.03.23 |
---|---|
다이캐스팅 Die Casting - 장점, 단점 및 응용 분야 4 | 2025.03.20 |
기존 원자로 vs 소형 원자로 차이점 0 | 2025.03.12 |
세대별 원자로의 특징 0 | 2025.03.12 |
바텀 업 설계 Bottom−UpDesign 2 | 2025.02.03 |