딥 드로잉 Deep drawing
2024. 11. 21. 02:18ㆍ과학-기구
반응형
딥 드로잉Deepdrawing은 금형 성형 공정의 일종으로, 평평한 금속 플랭크를 펀치와 다이를 이용해 원하는 형상으로 변형시키는 성형법입니다. 이 공정은 주로 원통형이나 상자 모양의 깊이가 있는 중공 부품을 제작하는 데 사용됩니다.
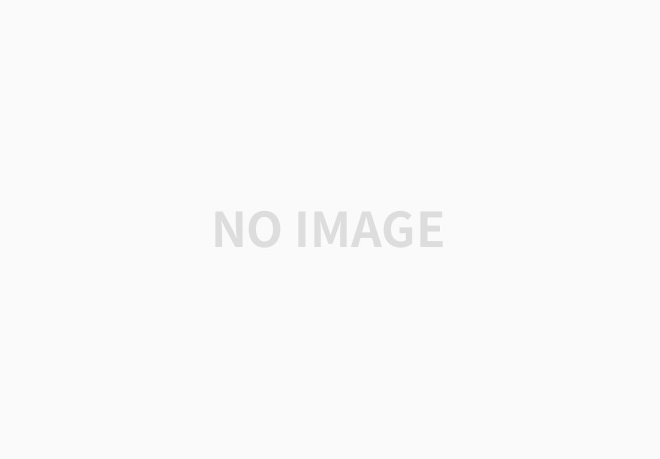
딥 드로잉의 원리
딥 드로잉은 금속 블랭크가 유압 구동 펀치에 의해 다이 캐비티에 강제로 들어가는 냉간 금속 성형 공정입니다.
이 과정에서 금속은 펀치에 의해 다이 안으로 밀려 들어가며, 인장과 압축 응력을 받습니다. 딥 드로잉은 깊은 성형으로 간주되며, 이는 성형된 부품의 깊이가 직경보다 클 때 해당됩니다.
- 주요 요소
- 펀치와 다이 : 펀치는 금속 블랭크를 다이 안으로 밀어 넣는 역할을 하며, 다이는 원하는 형상의 캐비티를 제공합니다.
- 블랭크 홀더 : 블랭크를 고정하여 주름 발생을 방지하고 균일한 성형을 돕습니다.
- 간극 : 펀치와 다이 사이의 간극을 소재 두께의 7 ~ 20% 정도로 설정되며, 이는 소재의 강도 및 가공 정도에 따라 달라집니다.
딥 드로잉의 공정 단계
- 블랭크 절단 : 금속판을 원하는 형상원형,사각형등으로 절단합니다.
- 다이에 블랭크 클램핑 : 절단된 블랭크를 다이에 고정합니다.
- 펀칭 : 펀치를 사용하여 블랭크를 다이 캐비티 안으로 밀어 넣습니다. 이 과정에서 블랭크는 점진적으로 변형되어 원하는 형상을 갖추게 됩니다.
- 제품 제거 : 펀치를 후퇴시키고 성형된 부품을 다이에서 제거합니다.
- 트리밍 : 필요에 따라 초과 블랭크를 잘라냅니다.
- 추가 공정
- 재드로잉Redrawing : 더 깊은 제품을 만들기 위해 이미 드로잉 된 제품을 다시 드로잉 하는 과정입니다. 이는 드로잉률이 0.5 이상일 때 필요합니다.
- 아이러닝Ironing : 벽 두께를 균일하게 하기 위해 벽의 두꺼운 부분을 얇게 만드는 가공입니다.
딥 드로잉의 종류
- 형상에 따른 분류
- 원형 딥 드로잉 : 가장 일반적인 형태로, 축 대칭 원주 모양을 가집니다. 재료가 원주를 따라 균일하게 변형되어 컵, 원통, 등의 형상을 제작합니다.
- 타원형 딥 드로잉 : 원형 대칭이 아닌 타원 형태의 제품을 만듭니다. 표면의 크기에 따라 정도가 달라집니다.
- 직사각형 딥 드로잉 : 직사각형 형태의 부품을 만듭니다. 단변과 장변 영역의 변형 정도가 다르므로, 재료 보충을 고려해야 합니다.
- 구형 딥 드로잉 : 구형 또는 반구형 제품을 만듭니다. 재료의 일부만 펀치와 접촉하므로 국부적 얇아짐이나 주름 발생에 주의해야 합니다.
- 원뿔형 딥 드로잉 : 깊이가 큰 원뿔 형태의 제품을 만듭니다. 재료의 변형력이 부위마다 다르므로 단계적 성형이 필요합니다.
- 공정 방식에 따른 분류
- 싱글 액션 딥 드로잉 : 금형이 한 방향으로만 움직이는 간단한 방식입니다. 구조가 단순하지만 복잡한 형상 제작에는 한계가 있습니다.
- 바이필라 딥 드로잉 : 펀치와 블랭크 홀더가 독집적으로 움직여 재료 흐름을 더 효과적으로 제작할 수 있습니다. 복잡하고 정밀한 부품 제작에 적합합니다.
- 다단 딥 드로잉 : 여러 단계를 거쳐 점진적으로 최종 형태를 만듭니다. 복잡한 형상이나 깊은 부품 제작에 사용됩니다.
- 리드로잉 : 이미 딥 드로잉 된 제품을 다시 한번 드로잉 하는 방식입니다. 더 깊은 형상이나 정밀한 치수를 얻기 위해 사용됩니다.
- 역방향 딥 드로잉 : 이전 공정에서 드로잉된 제품을 반대 방향으로 다시 드로잉 합니다. 주름 방지와 재료 강도 향상에 효과적입니다.
- 특수 기법
- 플랜지 딥 드로잉 : 제품의 플랜지 부품을 먼저 드로잉 합니다. 압축 주름에 의해 성형 한계가 제한될 수 있습니다.
- 단계식 딥 드로잉 : 깊이가 다른 여러 단계로 나누어 성형합니다. 복잡한 형상이나 깊은 부품 제작에 사용됩니다.
- 표면 딥 드로잉 : 수직이 아닌 곡면 형태의 측벽을 가진 제품을 만듭니다. 외부 플랜지가 축소되고 성형 부분이 신장됩니다.
딥 드로잉의 장점
- 대량 생산에 적합 : 딥 드로잉은 금형과 도구가 설정되면 부품을 빠르고 효율적으로 대량 생산할 수 있습니다. 금속 코일이 연속적으로 공급되므로 생산 중단 시간이 거의 없고, 장기 생산 주기에도 적합합니다.
- 비용 효율성 : 초기 금형 투자 후에는 생산 비용이 낮습니다. 금형 비용은 일회성이며 부품의 수명 동안 사용할 수 있습니다. 대량 생산 시 단가는 다른 금속 가공 방법에 비해 경제적입니다.
- 복잡한 형상 제작 가능 : 딥 드로잉으로 제작된 부품은 이음새가 없어 누수 방지가 필요한 응용 분양에 적합합니다. 다른 금속 스탬핑 기술로는 불가능한 복잡한 형상도 제작이 가능합니다.
- 높은 정밀도 : 딥 드로잉은 매우 정확하고 정밀한 기준에 따라 부품을 생산할 수 있습니다. 정확성뿐만 아니라 이러한 정밀한 요구 사항을 부품마다 반복적으로 재현할 수 있습니다.
- 다양한 재료 사용 가능 : 딥 드로잉은 탄소강, 스테인리스 스틸, 황동, 구리, 알루미늄, 니켈 - 실버, 사전 도금 강철 등 다양한 금속을 사용할 수 있습니다.
- 재료 강도 향상 : 딥 드로잉과정에서 금속이 늘어나면서 유연성이 증가하여 부품의 강도가 향상됩니다. 이는 높은 신뢰성이 요구되는 응용 분야에 적합합니다.
딥 드로잉의 단점
- 높은 초기 설정 비용 : 초기 금형 및 설정 비용이 다른 금속 성형 방법에 비해 상대적으로 높을 수 있습니다. 형상이 복잡할수록 금형과 초기 설정 비용이 더 높아질 수 있습니다.
- 소량 생산에 부적합 : 딥 드로잉은 소량 생산에는 비용 효율적이지 않습니다. 프레스 설정에 시간이 많이 걸리고 숙련된 금형 제작자의 전문 지식이 필요합니다.
- 제한된 프로트타입 제작 능력 : 소프트 툴링을 사용하지 않기 때문에 프로토타입 제작이 항상 가능한 것은 아닙니다.
- 표면 변형 가능성 : 딥 드로잉은 때때로 주름, 늘어남, 찢어지과 같은 표면 변형을 일으킬 수 있습니다. 이러한 변형은 항상 눈에 띄는 것은 아니지만 외관에 영향을 줄 수 있습니다.
- 설계 제한 : 딥 드로잉으로 제작할 부품을 설계할 때는 금속 시트의 굽힘과 늘어남 한계를 고려해야 합니다. 이러한 제한 사항은 벽 두께, 모서리 반경 및 기타 특징을 결정할 때 고려해야 합니다.
- 복잡한 형상의 제한 : 매우 복잡하거나 급혁한 굽힘이 있는 부품은 딥 드로잉에 적합하지 않을 수 있습니다.
반응형
'과학-기구' 카테고리의 다른 글
압출 방법 - 직접 압출, 간접 압출, 충격 압출 1 | 2024.12.27 |
---|---|
큰 수의 법칙 , LLN 1 | 2024.12.26 |
압연 Rolling 0 | 2024.11.20 |
단조 Forging - 열간 단조, 냉간 단조, 온간 단조, 자유 단조, 형 단조 0 | 2024.11.19 |
단조 Forging 0 | 2024.11.18 |